Includes: Anti-Chatter Technology ACT, 2X faster cuts, 50% more power, variable speed, reverse operation and more.
Brake Lathe
Hunter AutoComp Elite®
The AutoComp Elite® on-car brake lathe from Hunter Engineering features a patented Variable-Speed Drive System and Anti-Chatter Technology.
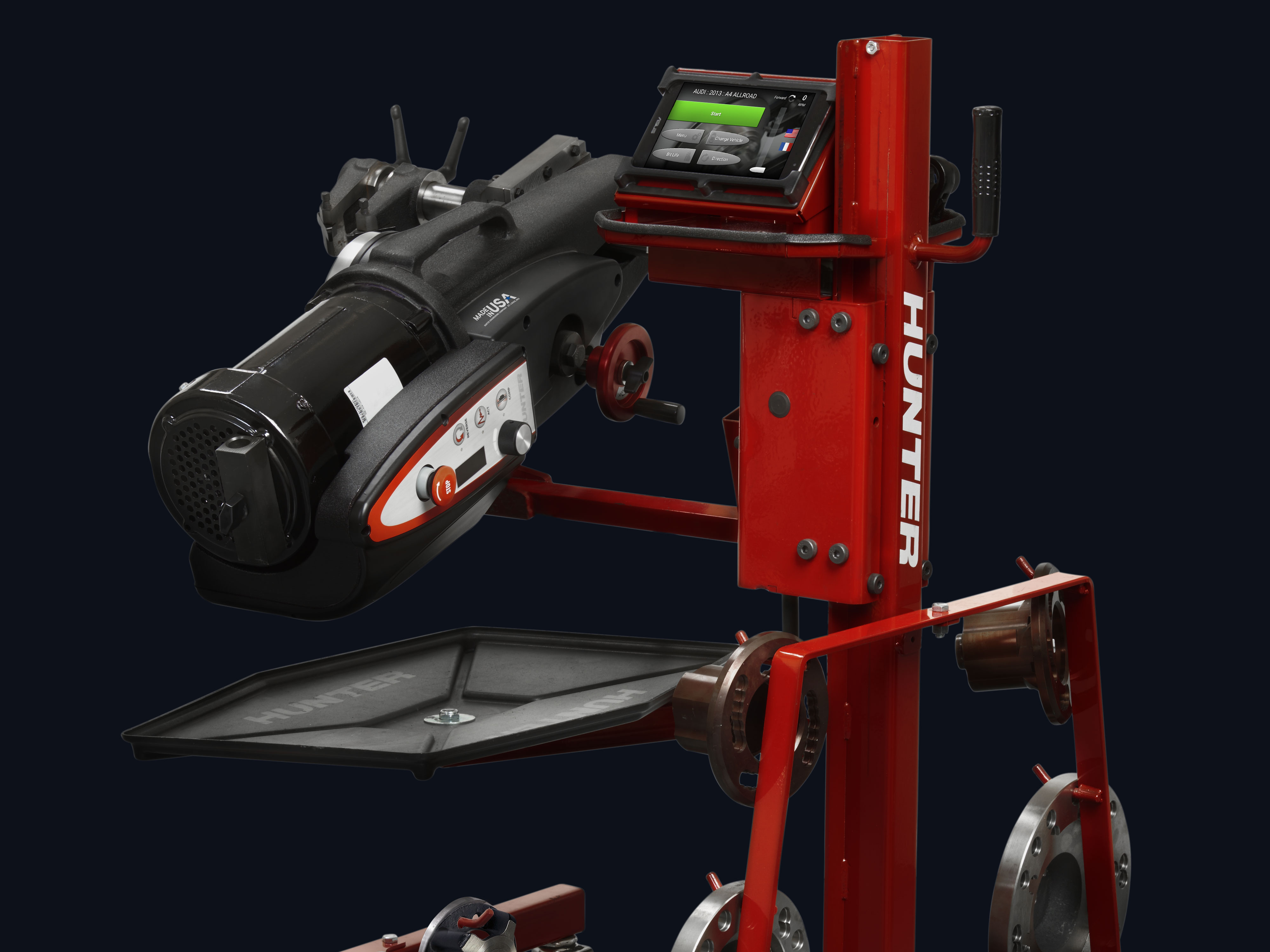
Hunter AutoComp Elite®
/
AutoComp Elite® At-A-Glance
50% more power cuts rotors twice as fast as other lathes
12 seconds or less average compensation time
Anti-Chatter Technology stops chatter before it starts
Touchscreen interface provides easy controls and additional info
Digi-Cal instantly measures rotor dimensions and depth of cut
Adaptors designed to fit any vehicle
Approved and recommended by multiple OEM partners
Fast brake service turns a profit for your business
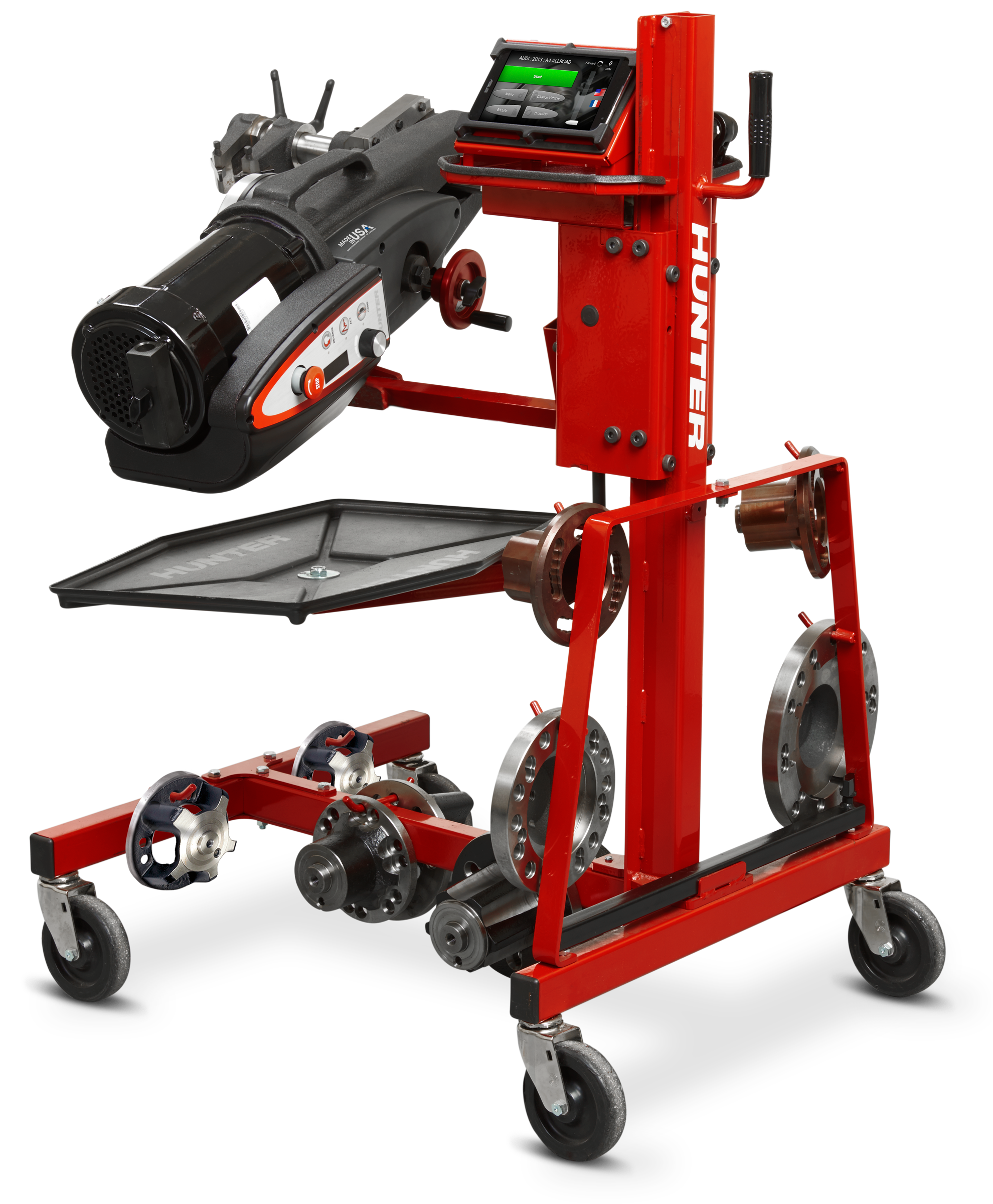
Intuitive Interface
Simplifies operation & "on-the-job" training with built-in training videos
Avoid Locking Differential Speeds
On trucks and performance vehicles
Up to 150 RPM
Allows you to cut approximately twice as fast as other lathes
Cut More Rotors
On high-drag vehicles
Directly Determines Compensation
And eliminates 'wandering'
Anti-Chatter Technology
Oscillates machining speed to prevent the buildup of vibration
1.5-HP Motor
Provides class leading speed and torque, avoiding the need to drop driveshafts
Adapter Look-Up
Find requirements and vehicle lug nut torque specs with the built-in database
Automatic Compensation
Directly determines compensation and eliminates “wandering”
Anti-Chatter Technology
Oscillates machining speed to prevent buildup of vibration (chatter)
2x Faster
Save up to 2 minutes per rotor and maximize service time
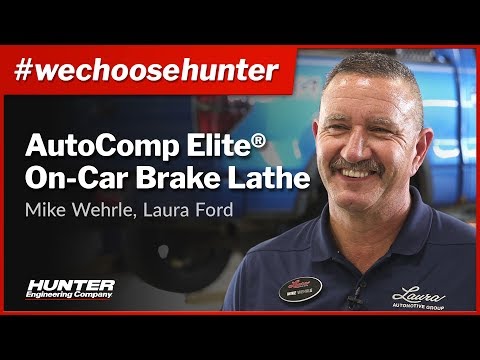
Hunter's AutoComp Elite® Brake Lathe at Laura Ford
Mike Wehrle, Service Manager at Laura Ford in Sullivan, MO talks about the superior surface finish and fast automatic compensation on rotor cuts they get from using the AutoComp Elite® brake lathe.
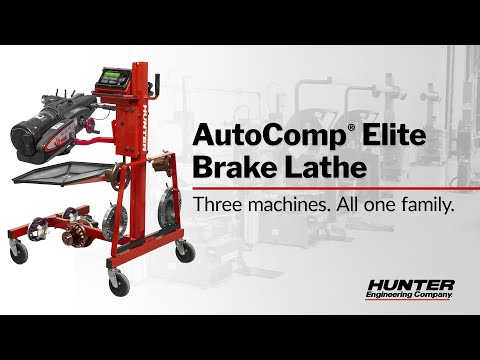
The AutoComp Elite® Family of On-Car Brake Lathes
The base AutoComp Elite® model combines its industry-leading cutting speed with automatic compensation for even greater performance.
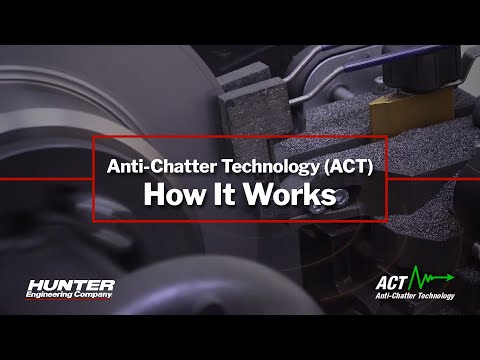
How ACT Works
An in-depth explination on how Hunter Engineering’s Anti-Chatter Technology (ACT) works on Hunter's BL Series Bench Lathe and the on-car lathe, AutoComp Elite®. This technology provides better brake rotor surface finish while also allowing the lathe to cut much faster.
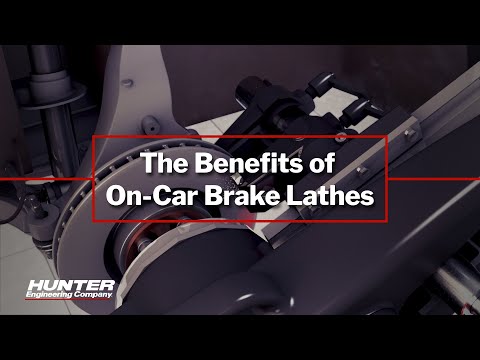
The Benefits of On-Car Brake Lathes
This video explores the causes of vehicle brake shudder and explains why resurfacing rotors on the vehicle provides a better, longer lasting brake job.
APPROVED AND RECOMMENDED BY MULTIPLE OEM PARTNERS
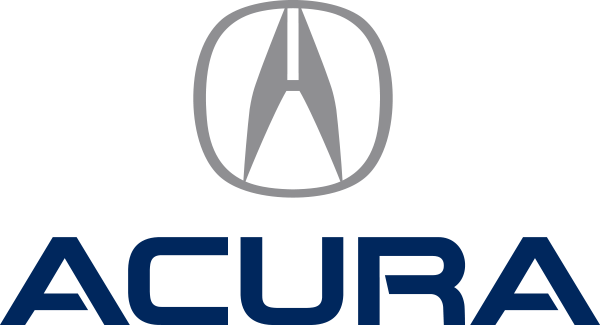
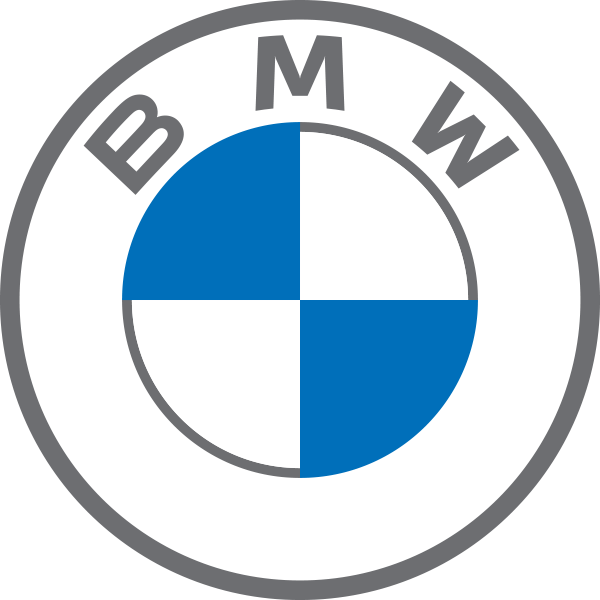
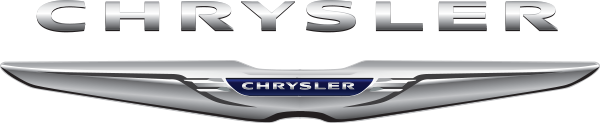
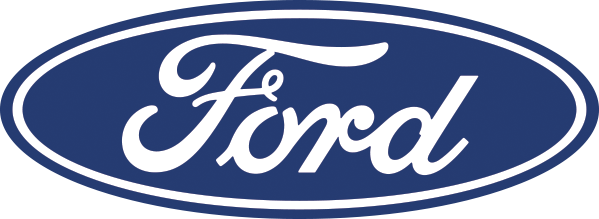
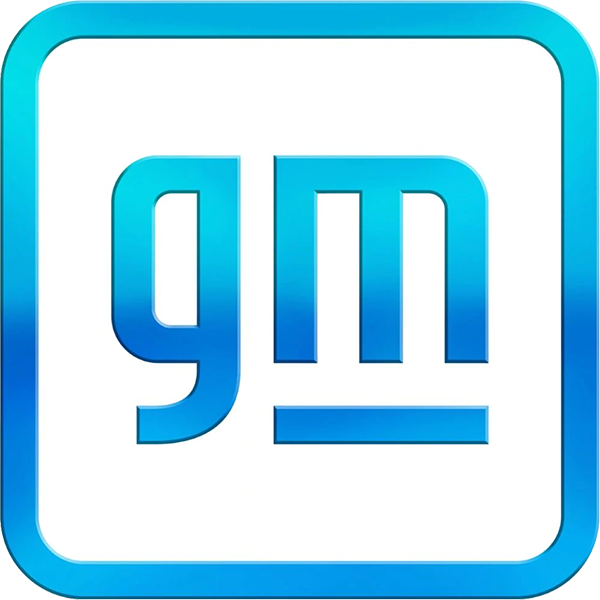
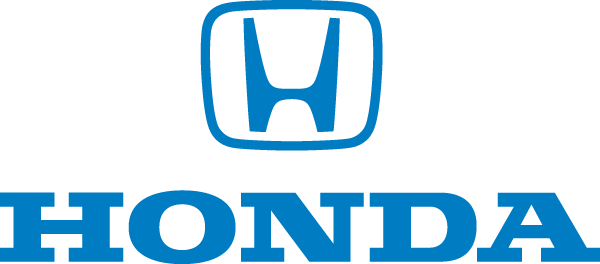


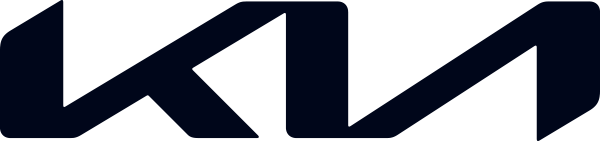
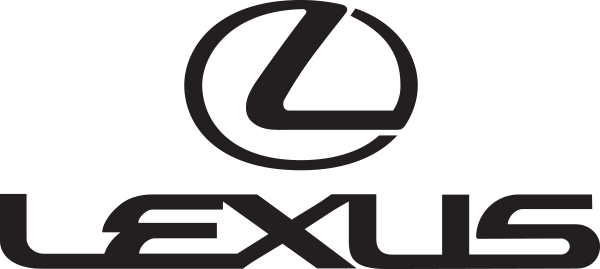
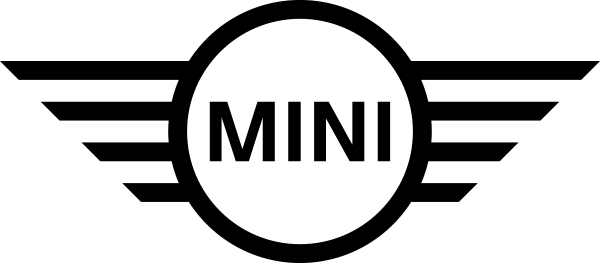
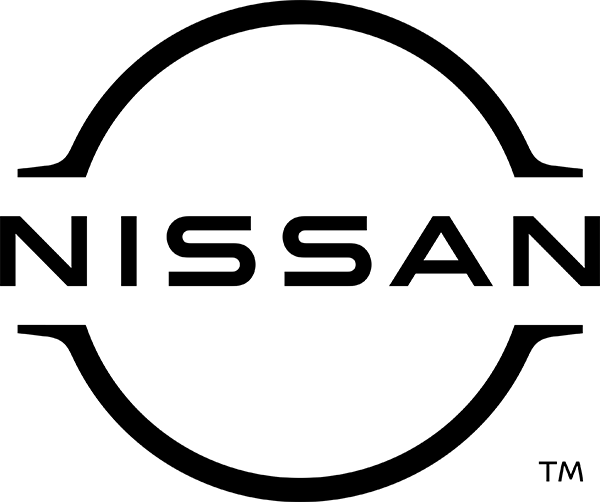
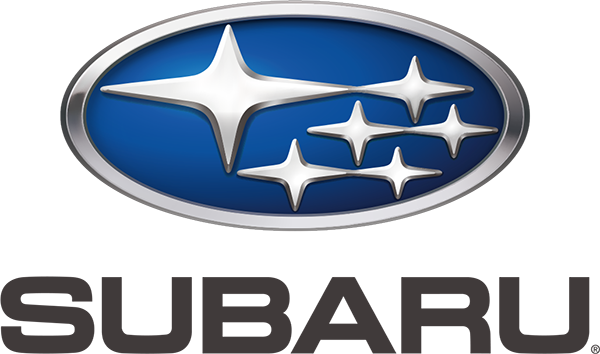
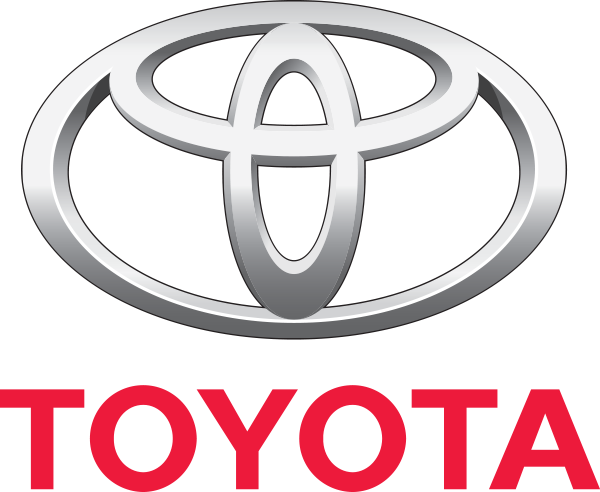
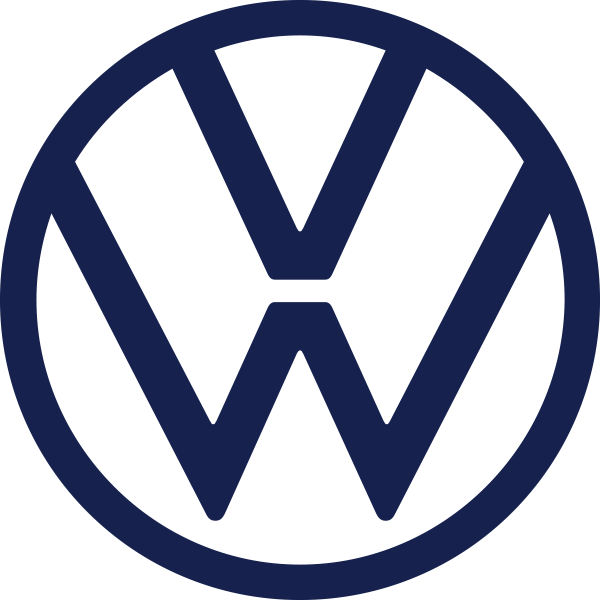
Autocomp elite® features
Convenient controls
Control lathe operation via the on-board control panel or tablet interface
Versatile control
Controls are always upright and easy to read on both sides
Bit Minder
Track cutting bit usage to ensure cut quality and minimize expense
Precision machining
Unique, stepped cutting pattern prevents radial "push-out" effect
Adaptor lookup
Database presents adaptor requirements as needed & vehicle lug nut torque included
Choose the best option for your shop
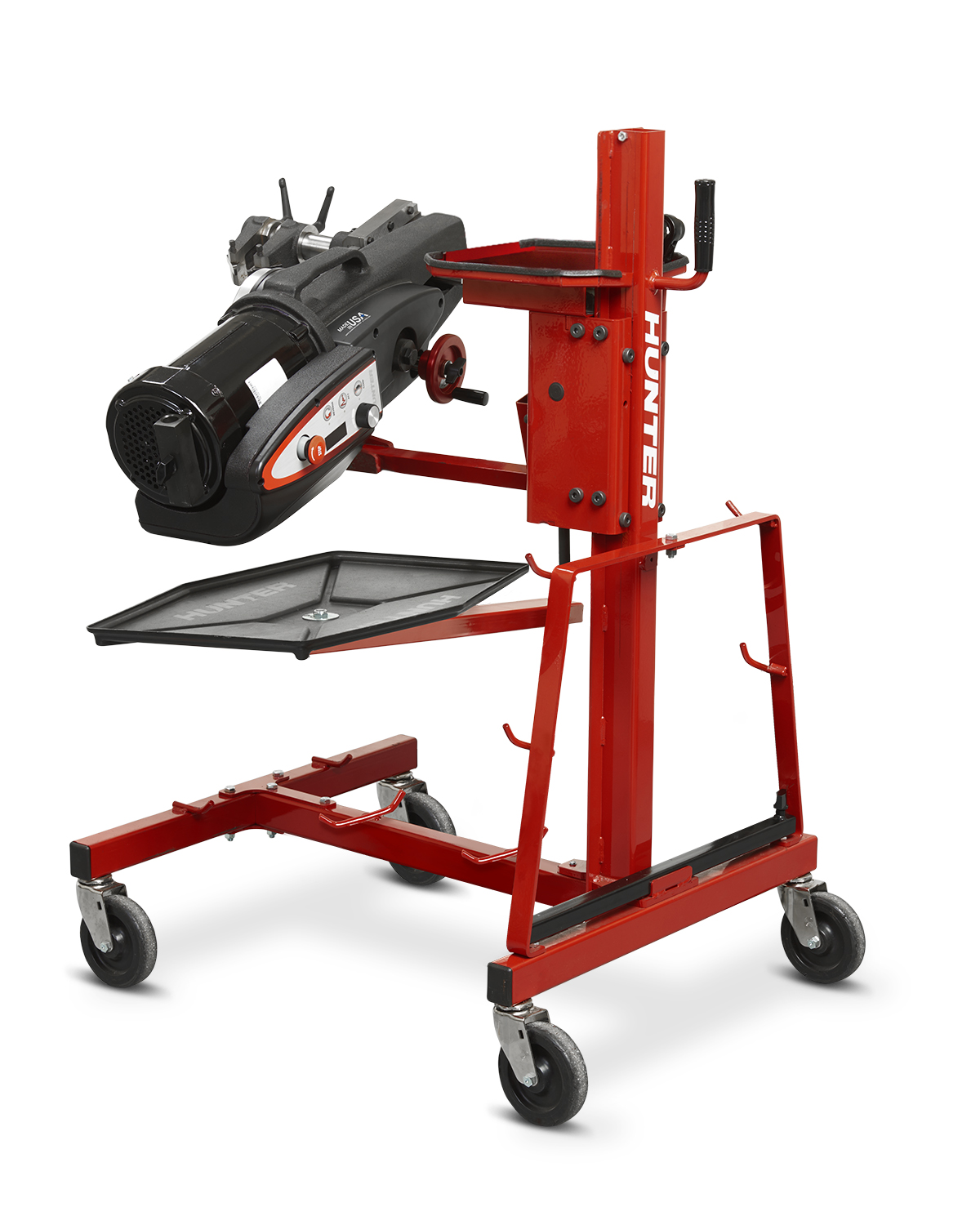
AutoComp Elite®
Base
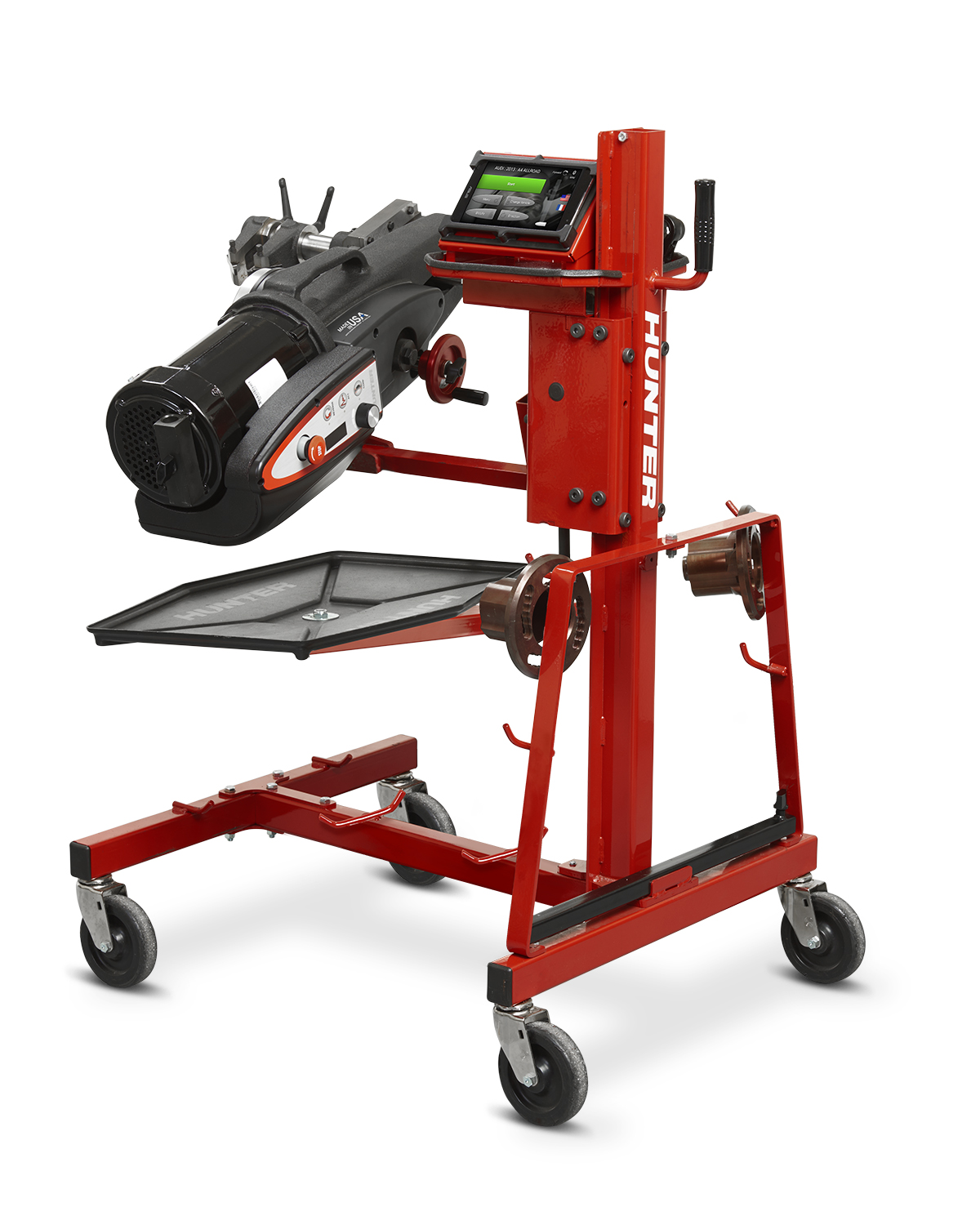
AutoComp Elite®
Standard
Includes: Base model features PLUS tablet interface, Vehicle spec database, BitMinder, Language support, training videos.

AutoComp Elite®
Digi-Cal
Includes: Standard model features PLUS Digi-Cal rotor measurement system which compares rotor thickness to vehicle specifications.
Anti-Chatter Technology stops chatter before it starts
Eliminate buildup of vibration
Anti-Chatter Technology varies the spindle speed to keep chatter-inducing vibration from starting, resulting in a smooth finish.
16 adaptors can be replaced by 5 adaptors
- 3,4, and 5 adaptors handle up to 3500 series trucks
- Handles 112mm through 210 bolt patterns
- Nearly 100% coverage up to 3500 series trucks with ext. twin cutter
Digi-Cal instantly measures rotor dimensions and depth of cut
Measuring system
Located in housing on the end of the cutter shaft.
LED lights
Bright LED light puts light where you need it - on the backside of the rotor.
Saving system
Does not lose calibration when turned off or stored.
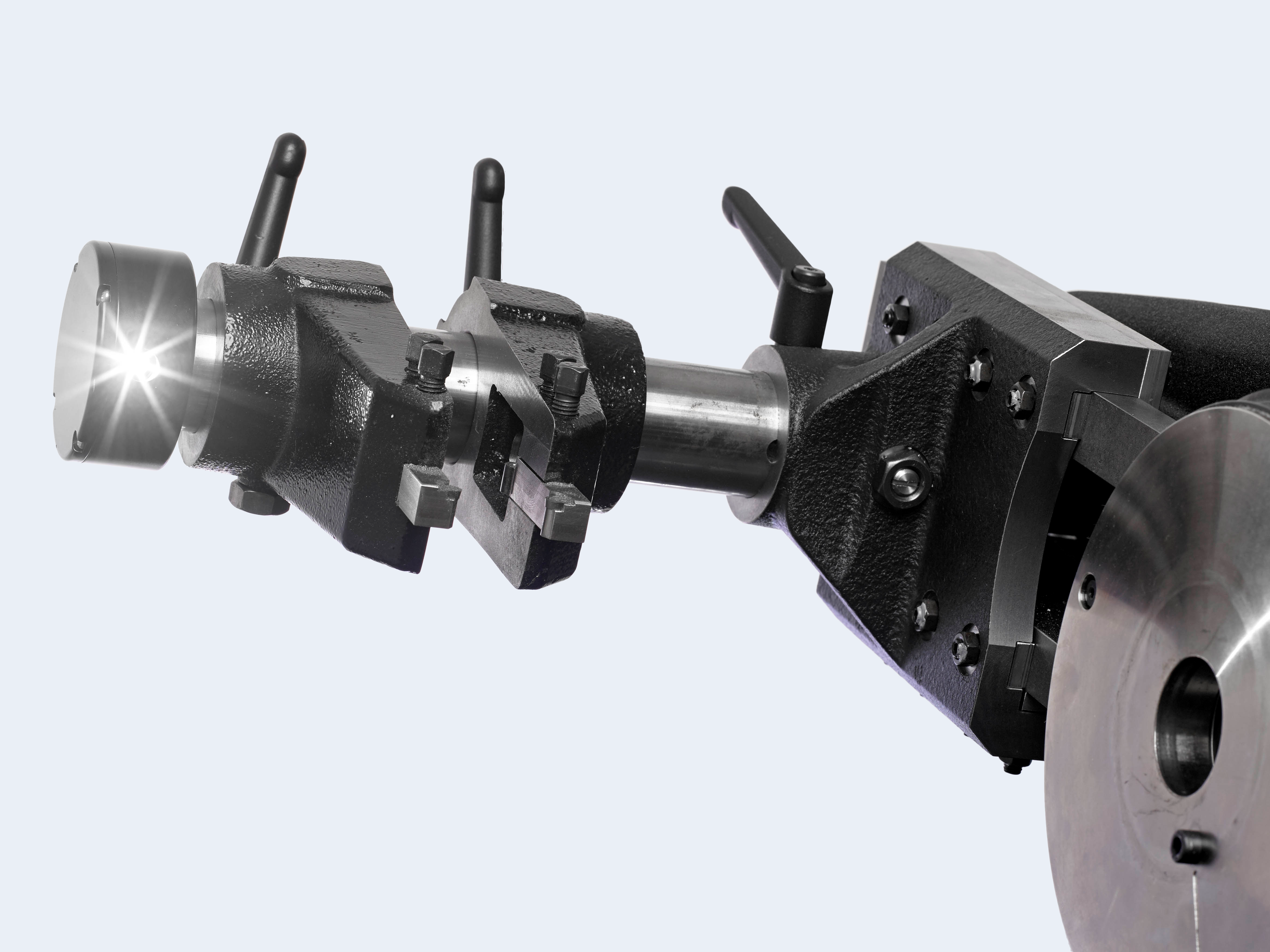
Easily service difficult vehicles
With superior performance features
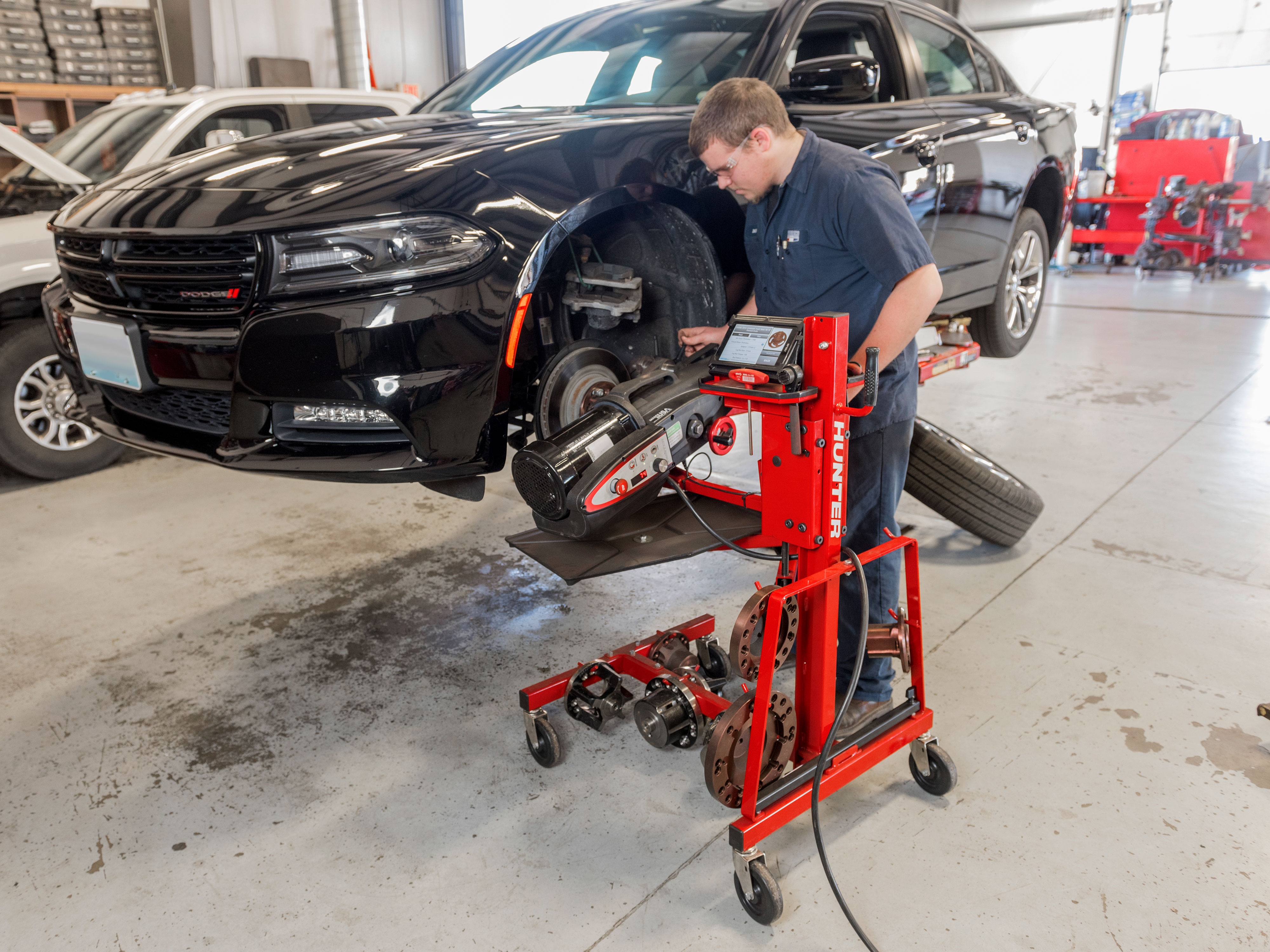
Automatic compensation “dials it in”
Eliminate guesswork by accurately calculating direct compensation
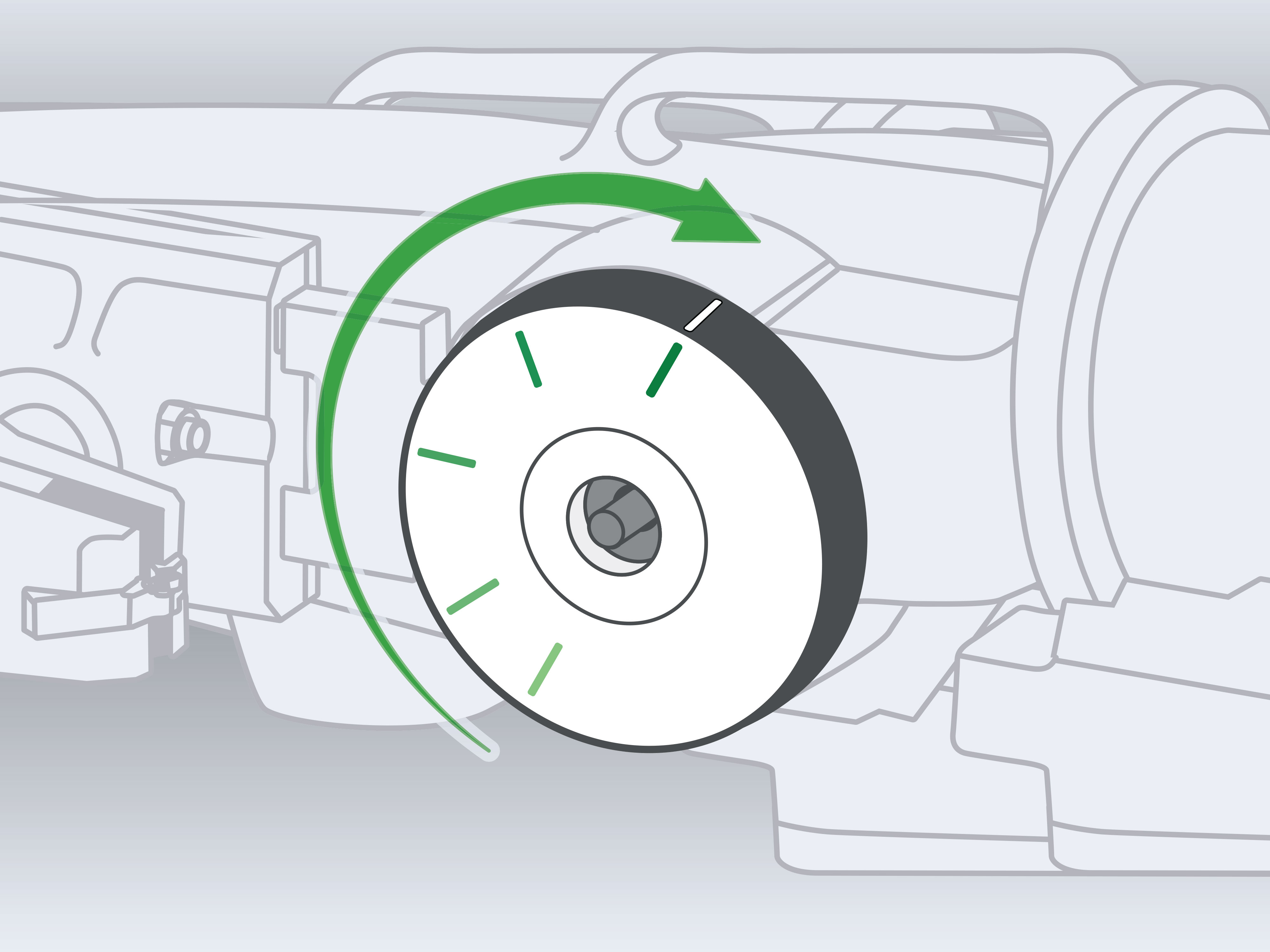
Having Trouble Deciding?
Here are some things to consider when choosing a brake lathe.
Watch in-depth procedure videos
Whether you're new or experienced, these AutoComp Elite® operations videos can fill in the gaps with tips and tricks on servicing brake rotors.
Use the Playlist button in the top-right corner to view all.
Easy viewing with Digi-Cal screen
Dimensions turn red when attempting to cut rotor below manufacturers specification.
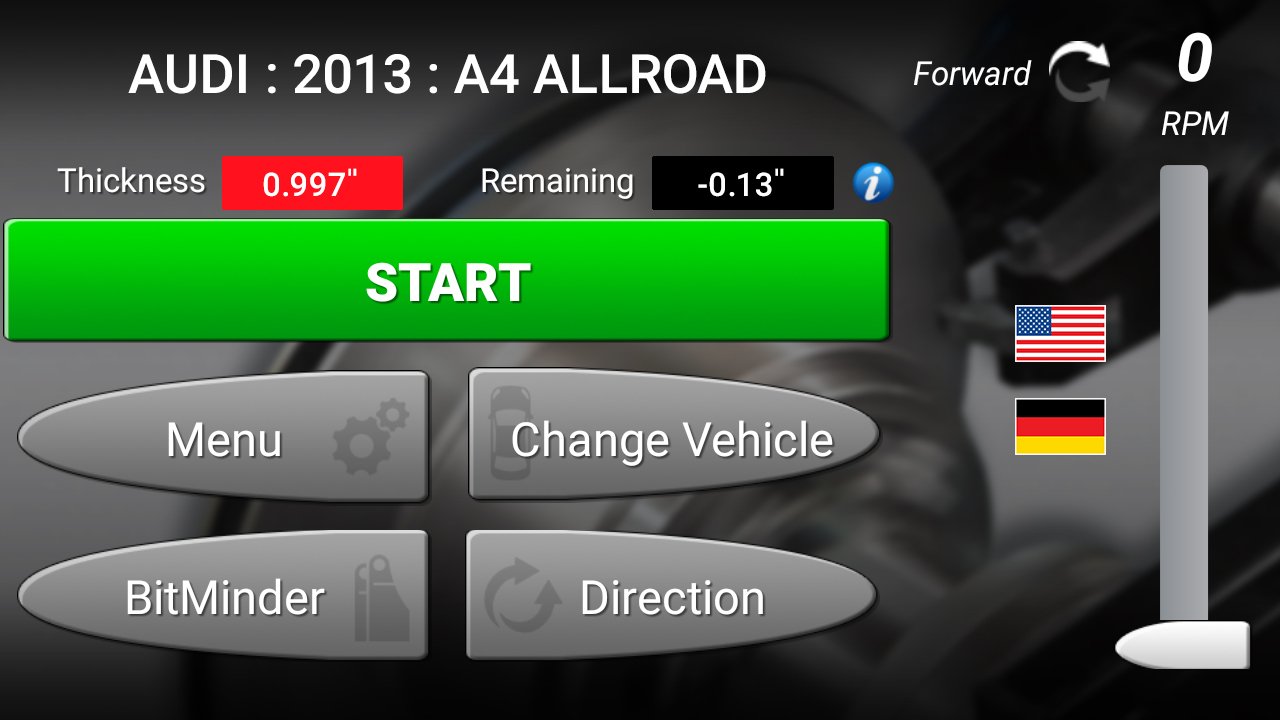
Are you ready to turn more profits with the AutoComp Elite®?
Contact your local Hunter representative for a free quote.
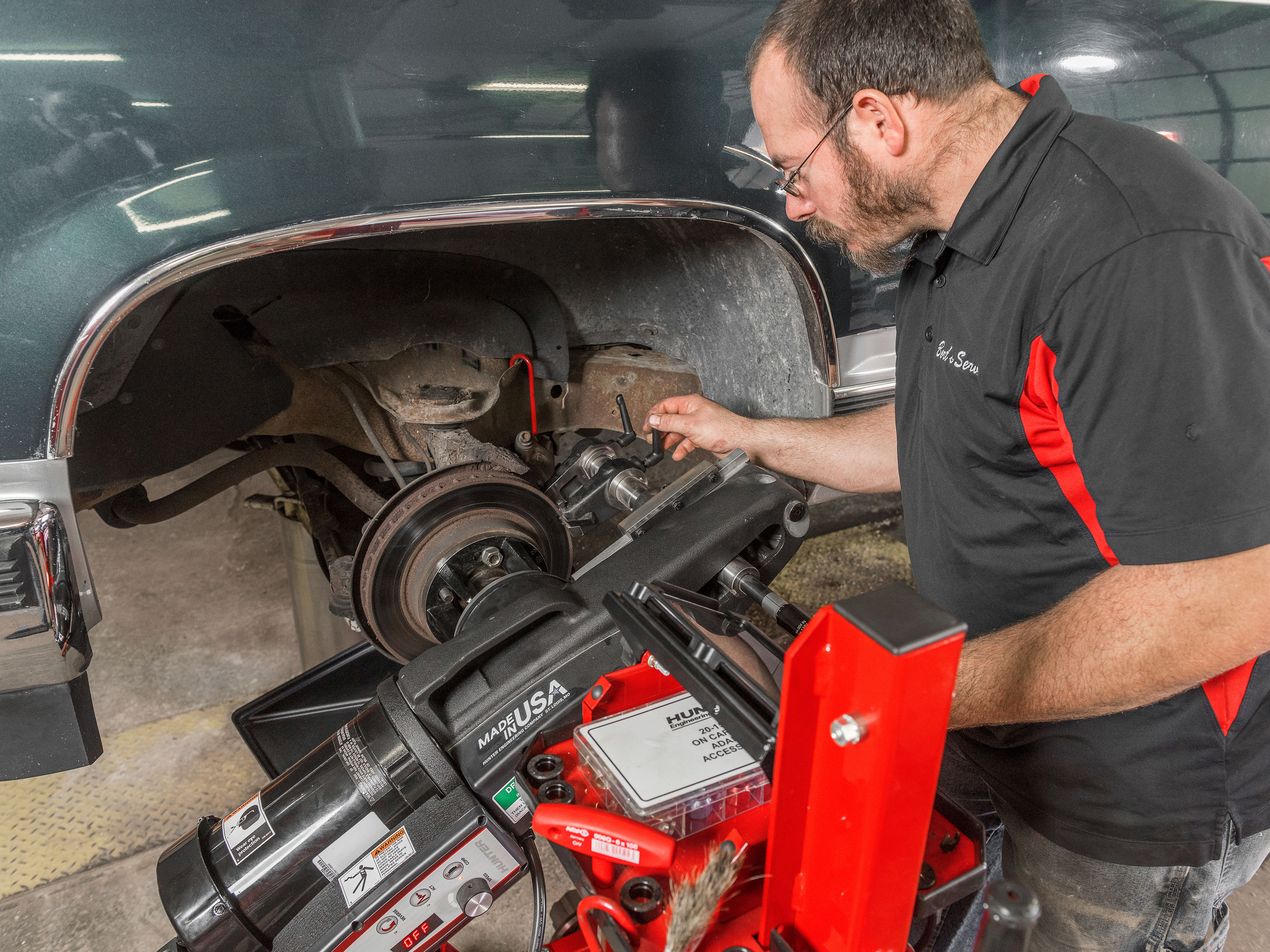
Specifications
|
|||||||||||||||||||||||||||||
---|---|---|---|---|---|---|---|---|---|---|---|---|---|---|---|---|---|---|---|---|---|---|---|---|---|---|---|---|---|
Gallery
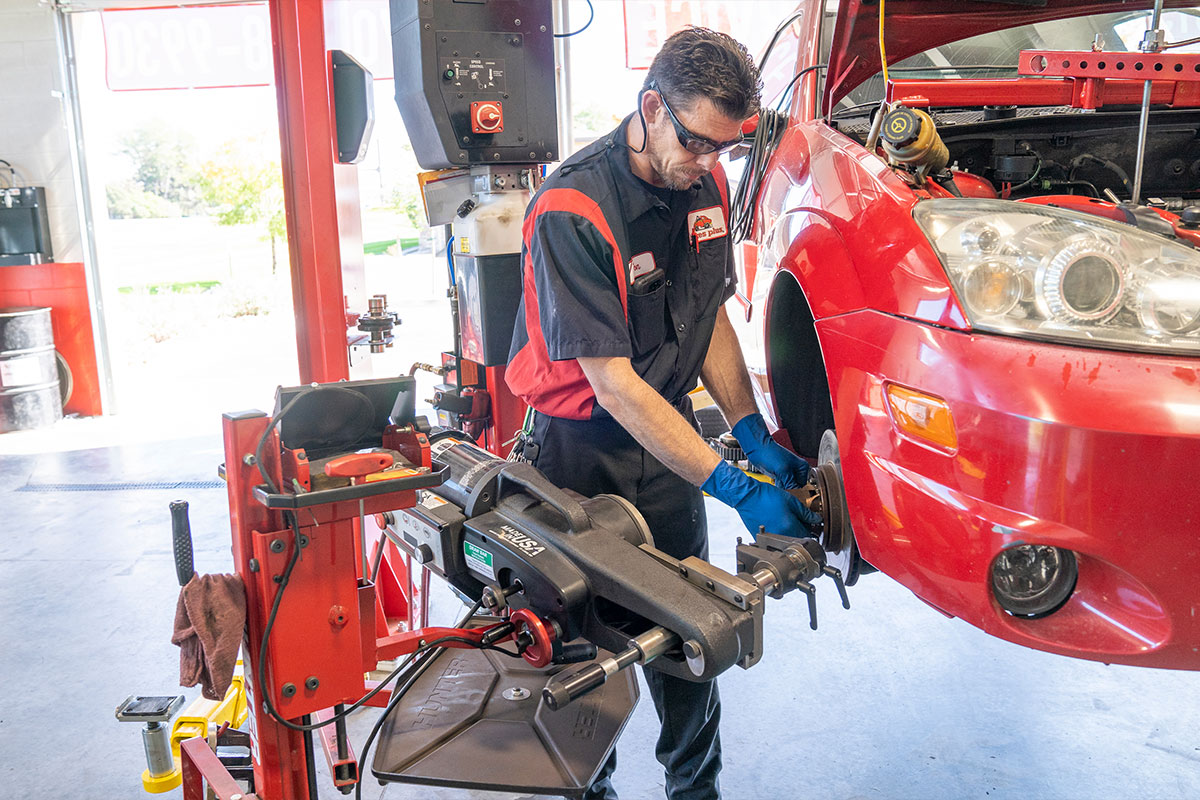
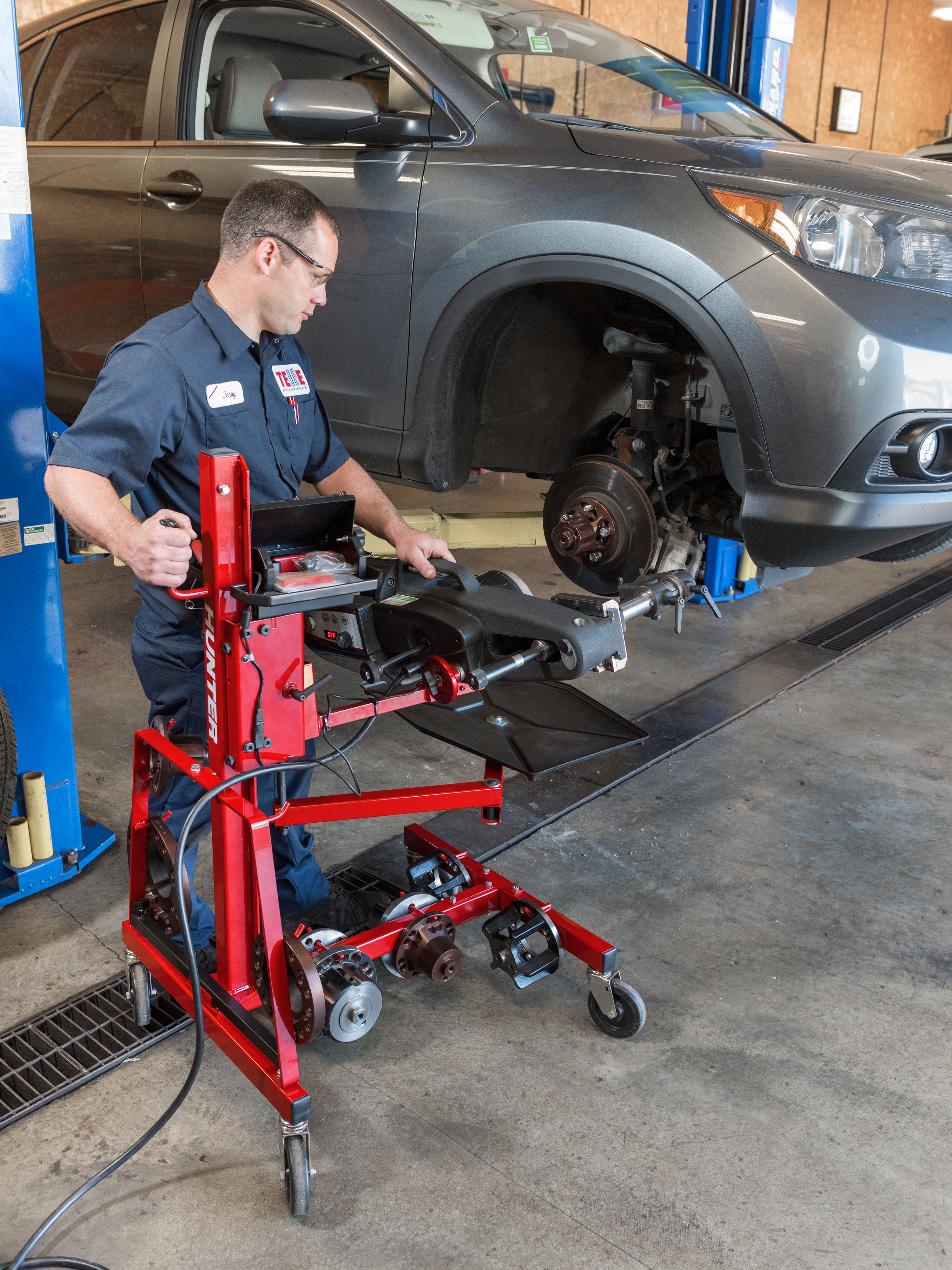
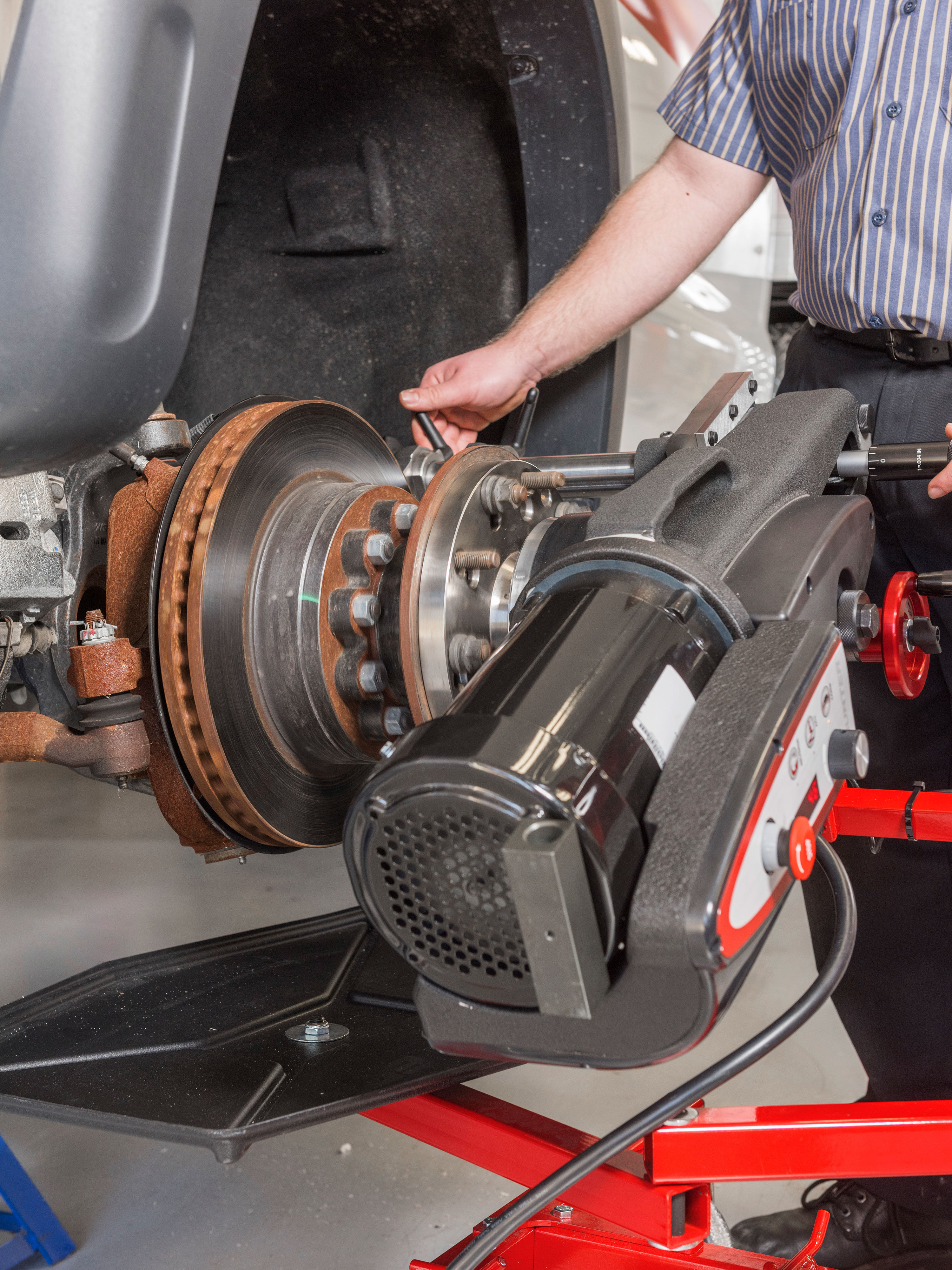
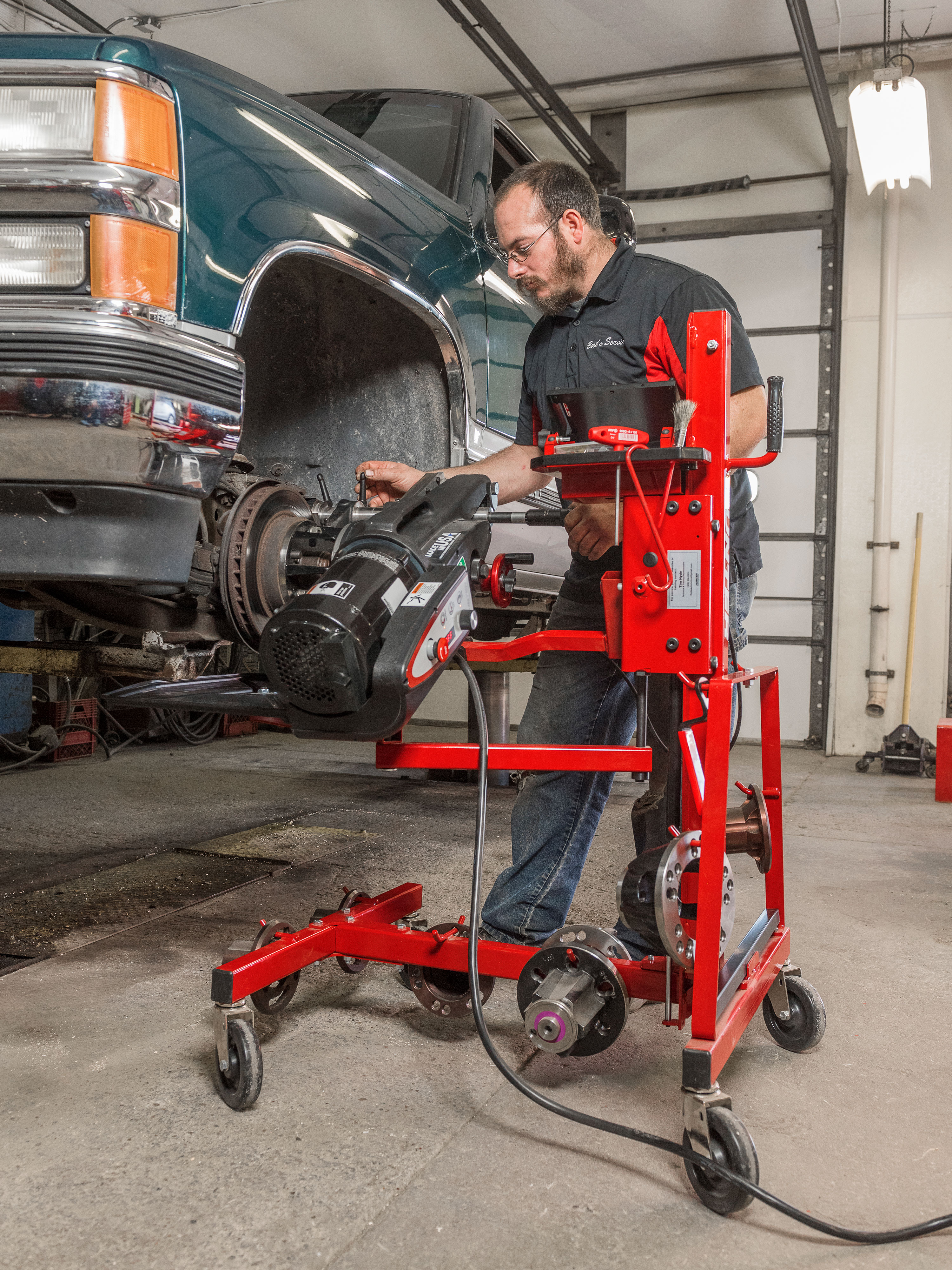
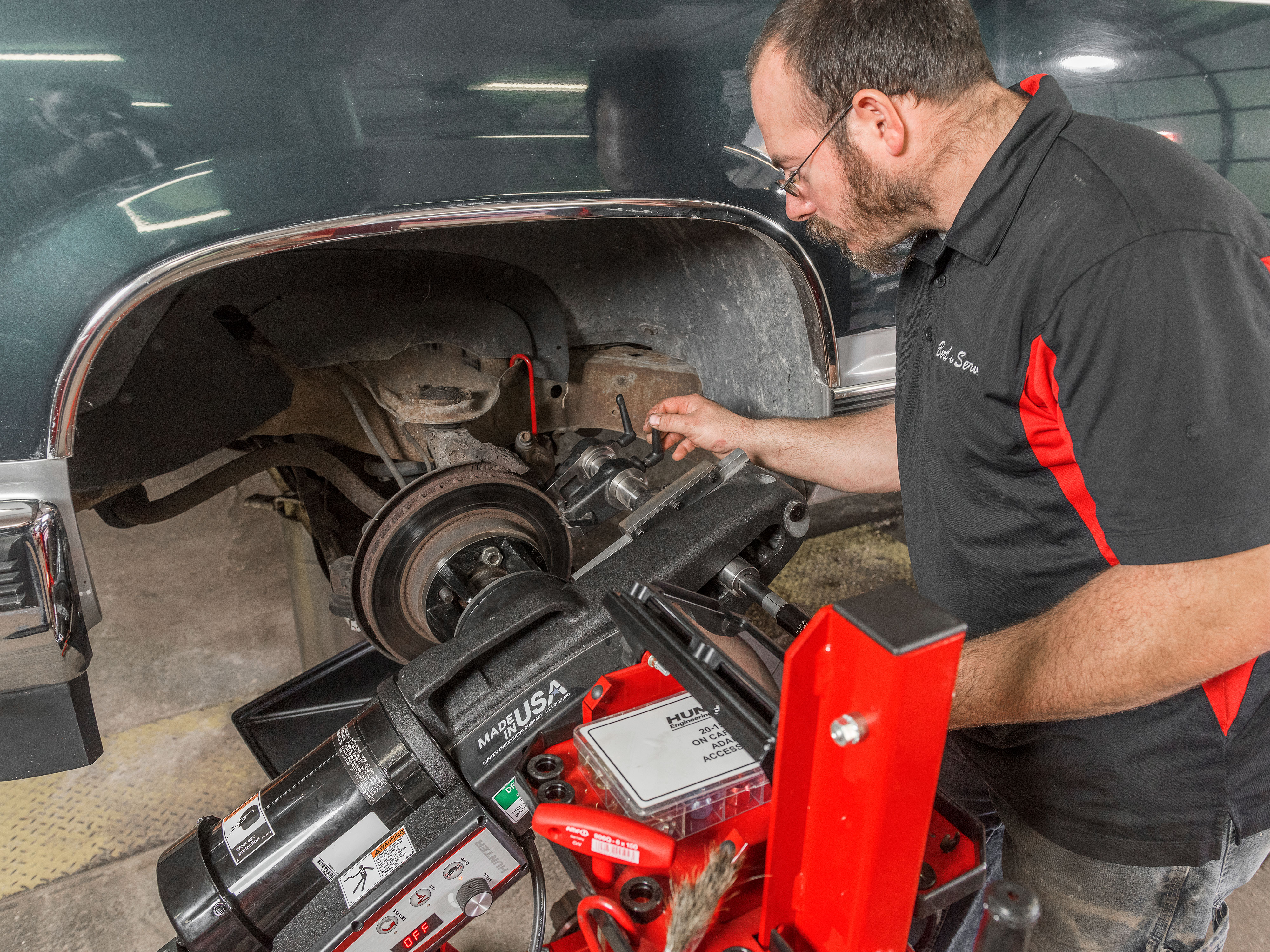
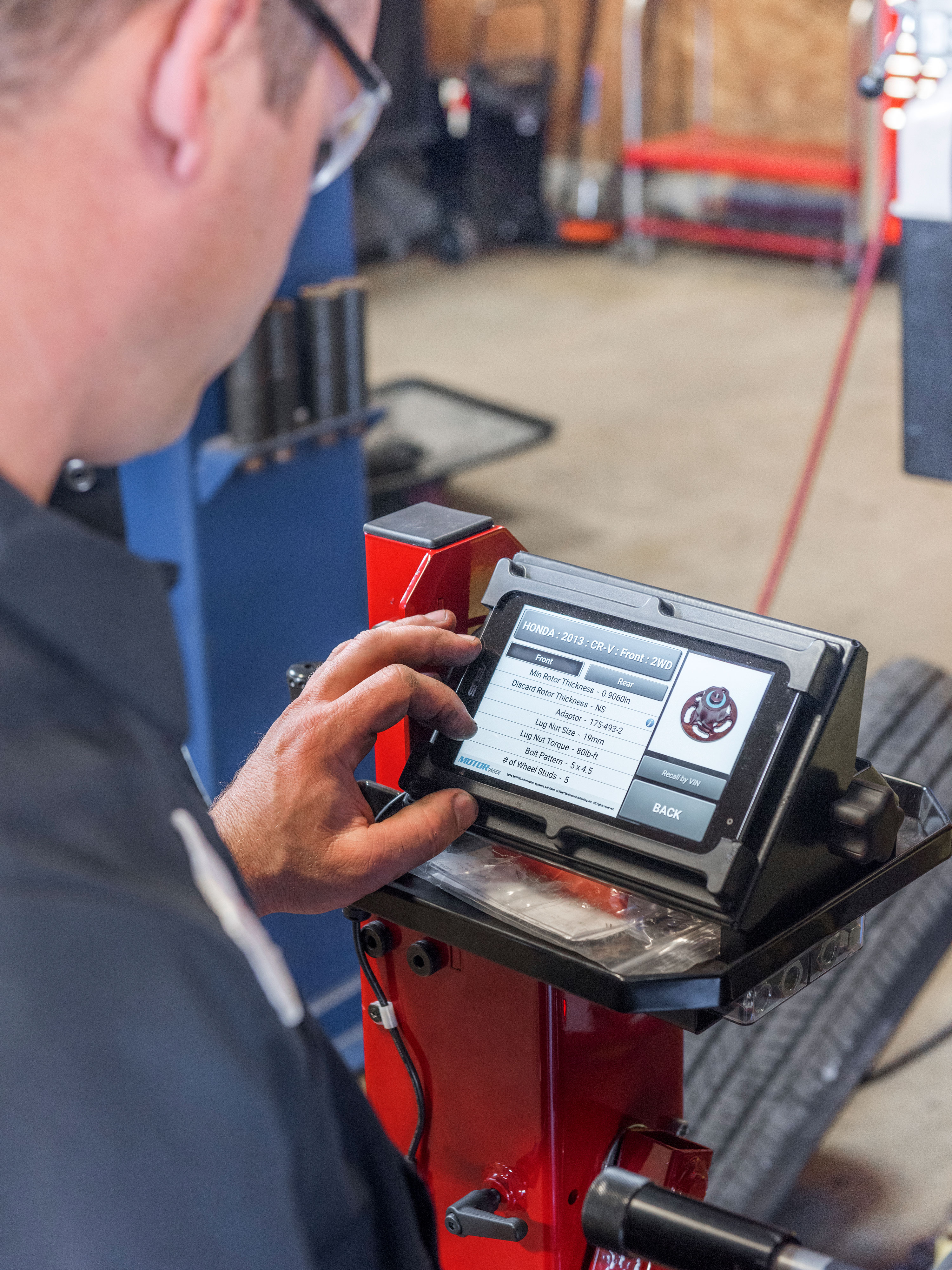
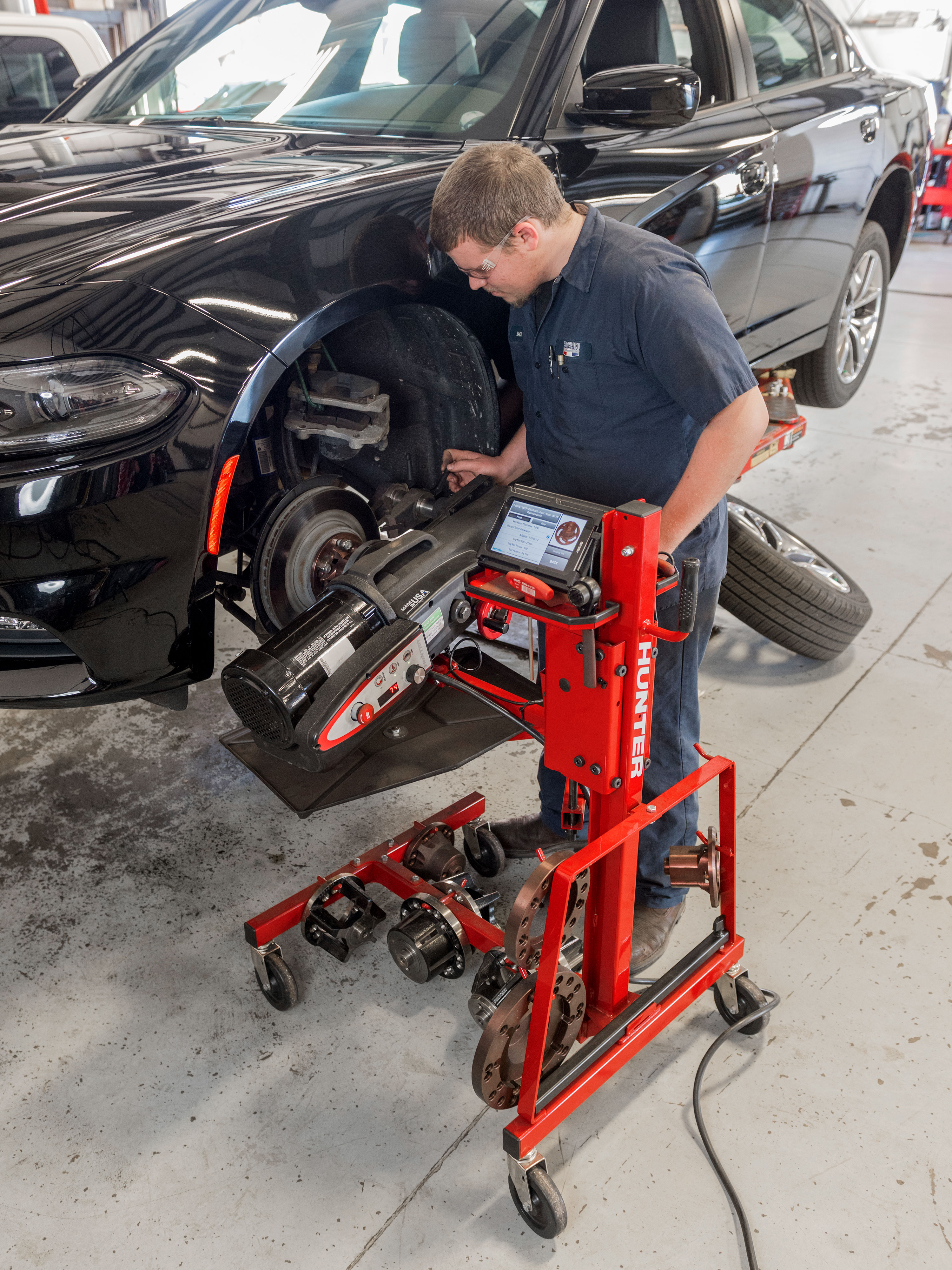
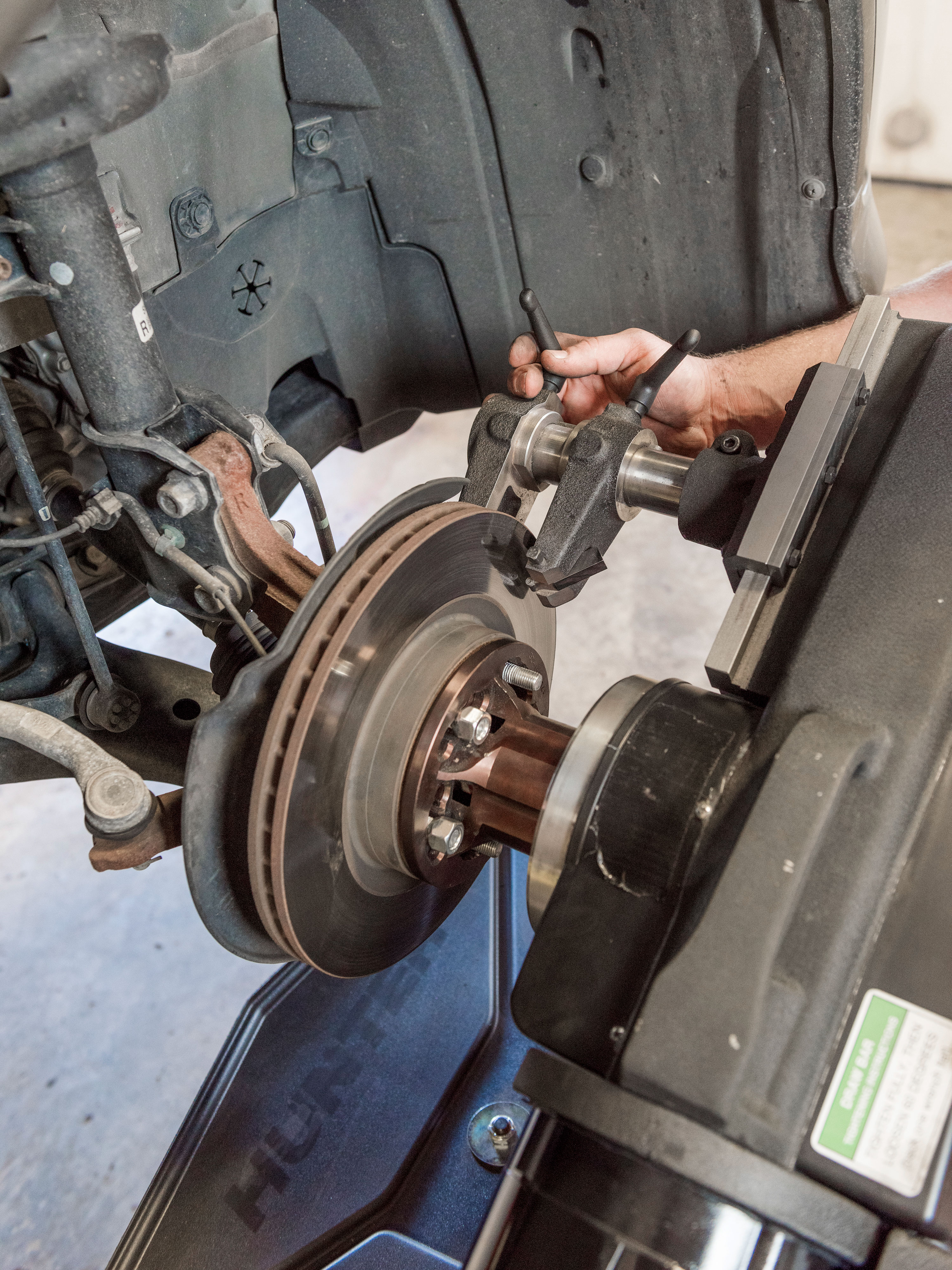
Because of continuing technological advances, features and configurations shown in customer photos may vary.
Hear what Hunter customers have to say
"Faster, easier, and much better setup."
Mike Wehrle, Service Manager at Laura Ford in Sullivan, MO, talks about the superior surface finish and fast automatic compensation on rotor cuts they get from using the AutoComp Elite® brake lathe.
"Service times reduced. Comeback issues eliminated."
Tim Smith, equipment manager at Brakes Plus, discusses technician satisfaction when using the AutoComp Elite®.
"I can’t stress enough the time-savings."
Craig Forman, Shop Foreman at BMW of Freehold in Freehold, NJ values the ease of training and operation of AutoComp Elite® for his team of 25 technicians.
"We can avoid differential lock-ups."
Justin Sailliez, Service Manager at Weeks Chevrolet Buick GMC in West Frankfort, IL speaks to their ability to handle difficult vehicles without the need to drop driveshafts.
Documents
-
Brochures
-
Specification Sheets
-
Accessories
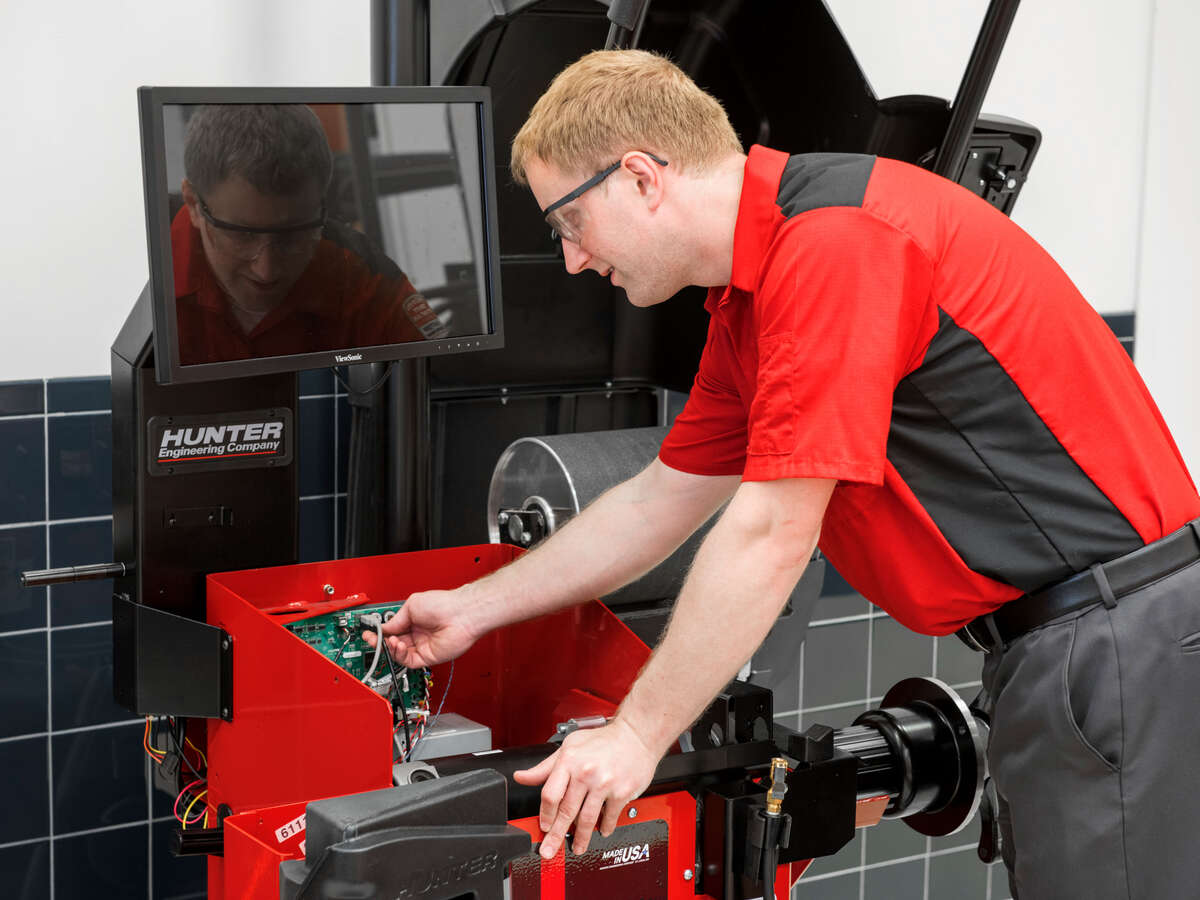
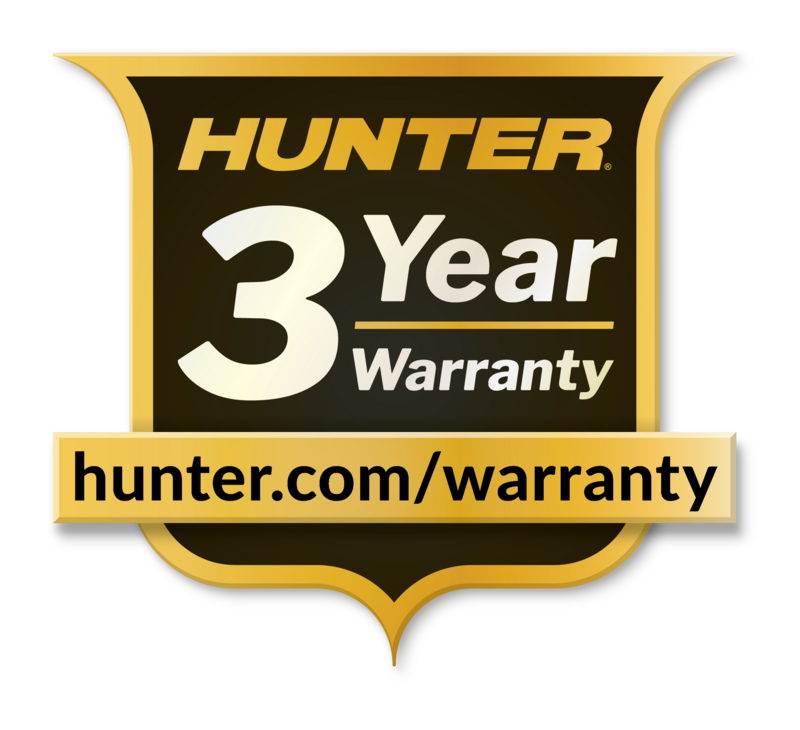
Hunter Engineering Company warrants new equipment replacement parts for three years and labor for six months.
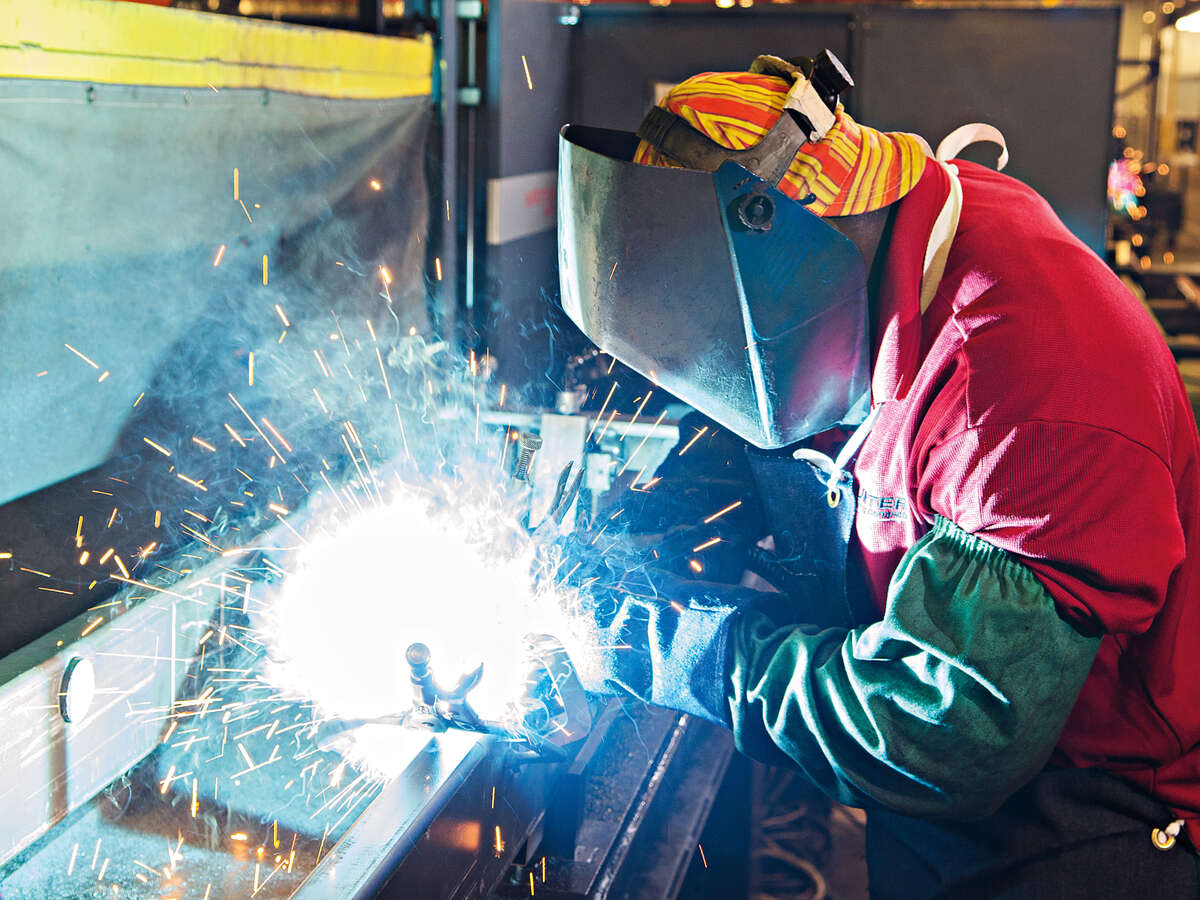
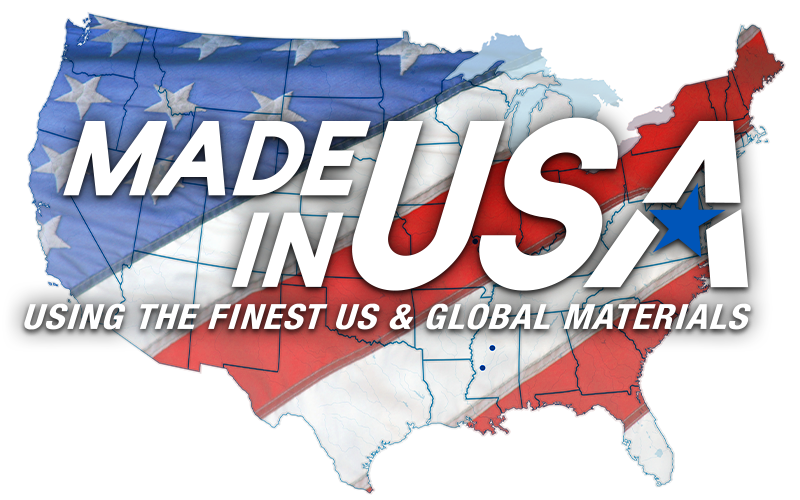
From raw steel to finished product. When you choose Hunter, you're investing in more than 1,000 American workers.